Project partners:
Aisin Automotive Casting, Kentucky, U.S. / aisinauto.com / production company
Econotherm, Wales, UK / econotherm.co.uk / technology supplier
Aisin Automotive Casting is a brand leader of engine-related functional parts and die cast parts in North America. Established in 1996, the Kentucky, U.S.-based company is part of the Aisin group companies, a Fortune Global 500 multinational company that primarily supplies engine, drivetrain, body and chassis and other automotive parts for Toyota and other OEMs.
As part of a comprehensive energy review, Aisin Automotive Casting was looking to reduce the running costs of its aluminum furnaces at its plant in Kentucky, U.S. After a period of technical consultation, the company selected Econotherm to provide an air-preheater based off a gas-to-air smooth pipe heat exchange design.
The original business case was approved on the basis of a $130,000 per annum saving against a total estimated project costs of $220,000. The installation was successfully completed by local contractors operating to an Econotherm outline design. The gas-to-air heat exchanger provided by Econotherm offered Aisin several benefits in this high-particulate exhaust environment which included:
Low fouling susceptibility due to smooth non-finned design
Ease of maintenance, as the pipes can be simply removed for cleaning
High reliability through multiple redundancy design as each pipe operates independently so that a single pipe failure (in itself a rare event) will not incapacitate the unit

The overall installation design needed to be failsafe such that production would not be affected in the event the recovery unit needed to be switched off. To address this challenge, Econotherm's engineers specified a solution which allowed the unit to be simply by-passed for routine maintenance events using an innovative cost-effective approach that avoided the need for costly exhaust diversion valves.
A further challenge was the very small available space in the proximity of the furnace heat source. Econotherm's engineers addressed this through a design that accommodates the entire recovery unit installation outside of the production facility as seen in the illustration below.

An operational measurement against the pre-installation baseline indicated annual savings of approximately $150,000, which was 50% in excess of the original project target. This excellent result delivered a total payback period for the project of 16.2 months.
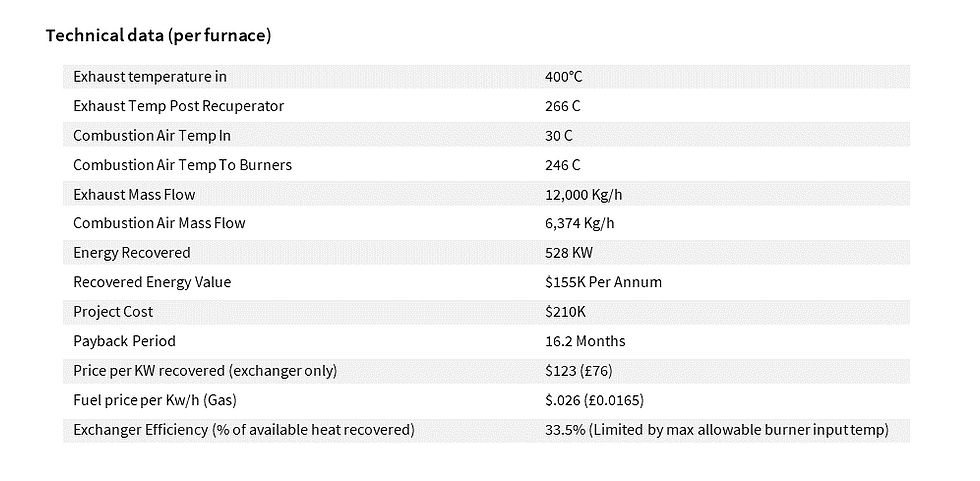
To learn more about Econotherm's gas-to-air heat exchange, email enquiries@econotherm.co.uk
Comments